Yamaha Motor Develops Hydrogen-Based Melting and Heat Treatment Facility
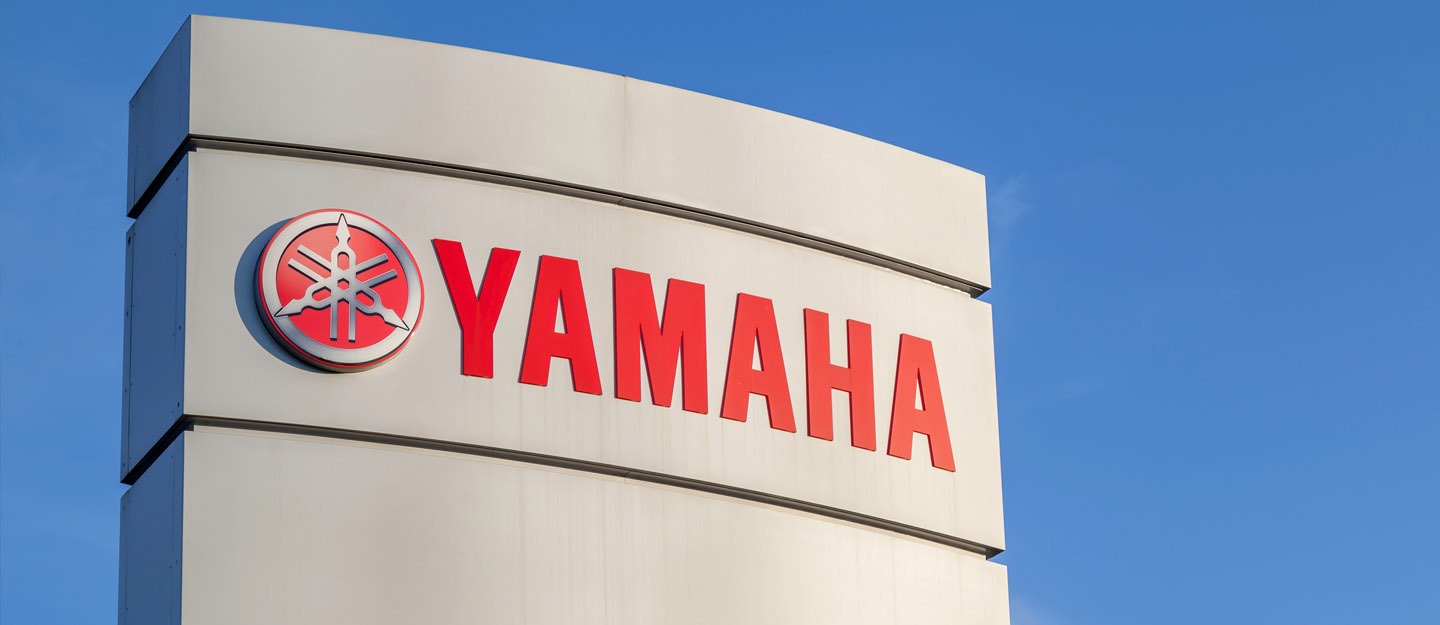
Yamaha Motor Corporation has announced the development of a state-of-the-art verification testing facility at its Morimachi Factory.
This factory is dedicated to hydrogen-based melting and heat treatment processes and the initiative aims to revolutionise aluminium alloy processing and to contribute to the company’s sustainability goals by reducing CO2 emissions.
Hydrogen-Powered Aluminium Processing
Yamaha will begin the development and verification of technologies for melting aluminium alloy using hydrogen gas in 2025. The facility will have a melting furnace and a heat treatment furnace, specifically designed for this purpose.
By the end of 2026, the company anticipates completing the development of these technologies, paving the path towards a gradual implementation at both domestic and international casting factories from 2027.
Green Hydrogen and E-Methane Production
Collaborating with Shizuoka University, Yamaha is exploring the equipment to produce green hydrogen and methanation equipment to create e-methane without relying on external heat sources. This initiative underscores Yamaha’s commitment to innovative and sustainable manufacturing practices.
This development is part of Yamaha’s broader strategy to minimise scope 1 CO2 emissions across its product line. The company has determined that hydrogen energy is more suitable than electrification for the melting process due to its high energy efficiency requirements.
Their focus on hydrogen energy aligns with their ongoing efforts to reduce its carbon footprint and enhance environmental sustainability.
Additional Hydrogen-Powered Innovations by YAMAHA
Yamaha unveiled a hydrogen-powered golf cart at the Yamaha Marine Innovation Centre. This golf cart, featuring two high-pressure, 25-litre hydrogen tanks, highlights their dedication to advancing hydrogen-powered transportation solutions.
Yamaha ensures the highest safety standards in its hydrogen projects as hydrogen safety is a critical concern.
The company adheres to rigorous protocols to manage risks, and hydrogen sensors and automated shutdown systems are incorporated to detect leaks and prevent accidents.
The industry plants follow stringent safety guidelines, including regular inspections and emergency response plans to handle potential hazards.
Its proactive approach to hydrogen safety and its continuous innovation in hydrogen technology demonstrate its leadership in sustainable industrial practices and clean energy solutions.