The Changing Landscape of Electrolysers for Green Hydrogen
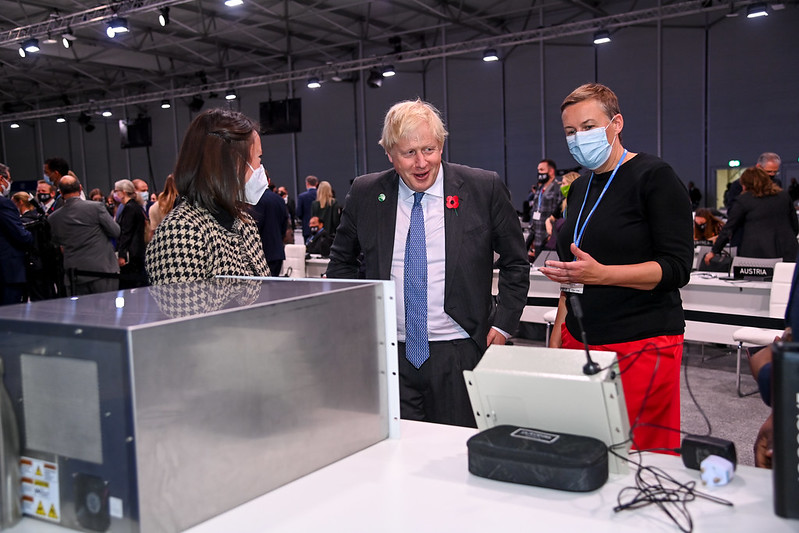
As investments in green hydrogen projects scale up across the globe, Hydrogen Industry Leaders look at how the landscape of electrolysers will change in the coming years.
As it currently stands, electrolysers are predicted to take a similar trajectory that wind and solar followed in terms of cost. According to a new report by the International Renewable Energy Agency (Irena): “The price of electricity procured from solar PV and onshore wind plants decreased substantially in the last decade. Thanks to the large pipeline of green hydrogen projects, a similar decline is expected for electrolysers in the coming decade.”
In the solar sector, the cost of modules fell 82% between 2010 and 2019, according to a 2020 Irena report, with onshore wind costs dropping by 39% in the same timeframe.
Lots of optimism surrounding Electrolysers for Hydrogen Production
Neal Dikeman, Partner at Energy Transition Ventures, spoke to Hydrogen Industry Leaders and highlighted: “We’re pretty optimistic about cost reductions in electrolysers. We’ve seen a large number of the players in electrolysis and seen where they believe costs can get to – and agree with the key assumptions.”
We certainly know the published forecasts and cost curves like everyone else. As volume grows, the costs are going to come down aggressively
If green hydrogen is scaled up to the required level to keep global temperatures 1.5 degrees above pre-industrial levels, 100 million tonnes of green hydrogen will need to be produced annually before 2030.
Adding to this, Neal said: “I don’t think the level of cost reduction is in question with scale, only the timing and the curve. The technology is there to do it. Frankly, the electrolyser companies are probably being conservative about what’s achievable when looking at the cost acceleration in solar PV and lithium-ion batteries.”
The real question is perhaps more on price and cycles than cost – will we see a temporary early oversupply of manufacturing capacity like in PV or an undersupply in capacity for a time, like in lithium-ion battery modules
Scaling up further, more than 400 million tonnes will be required by 2050, according to Irena. To meet these targets, a rapid fall in the price of electrolysers must arrive within the next ten years.
Cost reduction essential if the industry is to kick on with scaling up
Without a cost reduction, there is a real risk that the industry would fail to reach the 136GW production of electrolysers this decade.
90% of which would be alkaline electrolysers and 10% proton-exchange membrane (PEM).
Neal gave Hydrogen Industry Leaders exclusive insight into potential barriers that the industry faces. “It’s primarily manufacturing scale. For decades a few tens of MWs of electrolysers per year was a pretty large manufacturing capacity. It’s like solar a couple of decades ago and batteries 5 to 10 years ago; you can only reduce costs so much if you’re building in a small volume.
Electrochemistry-based products have responded very well to massive manufacturing volumes. Once you reach critical mass in manufacturing plant size, the industry knows how to improve processes, design for manufacturing, materials reductions, performance improvements, and supply chains for this type of product.
A few components may be tricky, such as noble metal catalysts, storage, integrated power electronics, etc. Still, we know of many companies working on those issues now – and there are many ways to get this done
There is an Alkaline vs PEM debate – but clearly there is no silver bullet
Advocates of PEM technology argue that it is better able to cope with the ups and downs of variable renewable energy than alkaline electrolysers, but Irena does not seem to agree.
“The flexibility of alkaline and proton-exchange membrane stacks [inside electrolysers] is sufficient to follow fluctuations in wind and solar,” it says.
Irena also warns that PEM electrolysers “may encounter a significant supply risk”, whereas more conventional alkaline machines would not.
“Meeting the required capacity [for PEM electrolysers] by 2030 will require mining of critical materials like titanium (5,500 tonnes), iridium (9 tonnes), and platinum (5 tonnes),” the report says. “However, improved design and raw material efficiency in PEM electrolysers can cut demand by up to 90% from current levels.”
Energy Transition Ventures have just backed a PEM electrolyser company called Ohmium and are bullish on PEM being able to win at a world scale on cost and performance. It has proven effective at reducing upfront costs and continues to work on the issues related to efficiency, system size, and operating performance. But the conventional alkaline community is not done.
Rounding up, Neal told Hydrogen Industry Leaders: “We’ve been following many emerging AEM technology companies and research; we think AEM is the best thought of as an alkaline variant, though that technology is still very young. The overall green hydrogen market is functionally uncapped in scale, so we may see a range of technologies do fine.”