STEGRA Leading Sweden’s Hydrogen Revolution
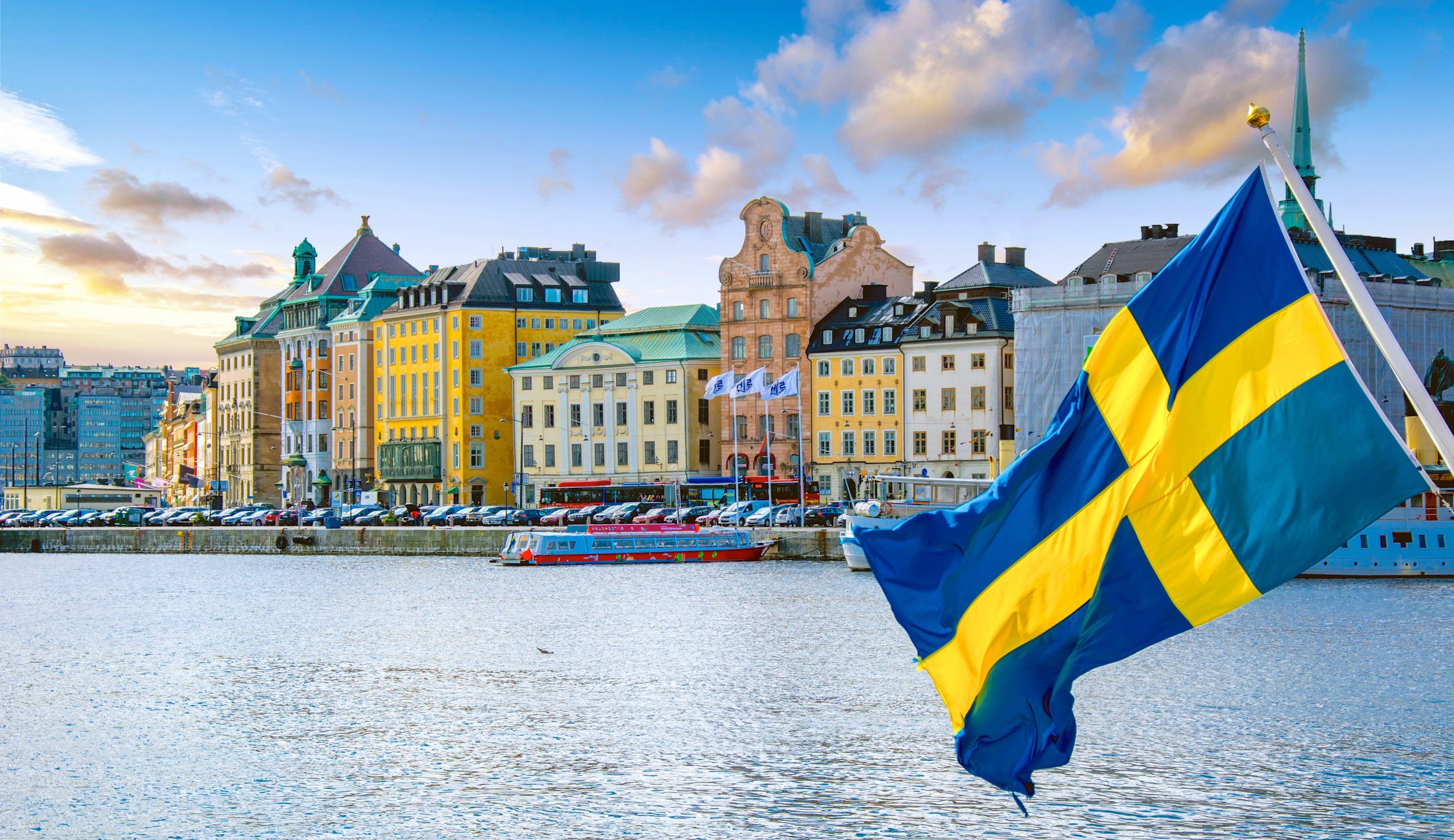
Swedish company ‘STEGRA’ is making significant steps in green hydrogen and steel production, recently securing a significant grant from the Swedish Energy Agency’s “Industrial Leap” program. The funding will support their flagship project, a large-scale green-hydrogen steel plant in Boden, which aims to revolutionise the industry with near-zero emissions.
STEGRA has been at the forefront of innovation, integrating green hydrogen in their processes to drastically reduce CO₂ emissions in steelmaking. Their work is pivotal in setting new standards for sustainability across Europe’s heavy industry.
STEGRA secure 100m EUR grant
Today, (19/09/24), the Swedish Energy Agency has announced that local company, ‘STEGRA’ (previously known as H2 Green Steel) has been granted approximately €100 million from the state for its establishment of a fully integrated near zero-emission steel production facility in Boden.
Earlier this year, the European Commission approved, under the EU State aid rules, a €265 million Swedish measure made available in part through the Recovery and Resilience Facility to support STEGRA in setting up a large-scale green steel plant
These Swedish support programs are essential for the improvement and expansion of the hydrogen industry in Sweden. The funds from the state now signal that there is national backing for one of Sweden’s largest industrial projects. It also contributes to some levelling of the playing field with other steel companies in Europe that have received large support packages. This creates the prerequisites for STREGRA to build up a long-term sustainable and competitive industry in Sweden.
Henrik Henriksson, CEO of Stegra commented:
“Implementing change towards sustainable solutions in the steel industry has historically been slow and subsidies to the high-emitting incumbent players have been high. This is beginning to change with the revised Emission Trading System where the free allocation is gradually phased out, and the Carbon Boarder Adjustment Mechanism, which is phased in step by step. State aid can be used to help speed up change until those regulation changes are fully implemented, as well as to level the playing field between established players and new cleantech companies. For highest impact, state aid should be allocated to the most efficient projects”
“Swedish industrial companies have the potential to become world leaders while contributing to the green transition of society as a whole. Initiatives within the Industrial Leap are of great importance for both the climate and the competitiveness of our industry”
STEGRA’s Boden Plant
Stegra’s Boden plant represents a monumental step in the green steel industry, combining three plants together. By 2030, the plant aims to produce 5 million tonnes of green steel annually.
Located in northern Sweden, the facility will be the world’s first large-scale green steel plant, using hydrogen-based direct reduction, an alternative to traditional coal-driven methods. The process eliminates nearly all CO₂ emissions by replacing fossil fuels with green hydrogen, which is produced from renewable energy sources like wind and hydropower.
The plant’s importance extends beyond its technological advancements. It reflects a shift toward decarbonising one of the most emission-heavy industries in the world. Steelmaking, traditionally reliant on coal, is a major contributor to global greenhouse gas emissions
The Boden facility ties into a national effort to push forward industrial decarbonisation, aligning with Sweden’s long-term vision of becoming carbon neutral by 2045. The plant’s reliance on renewable energy sources ensures that its impact on carbon emissions remains low, while its integration with Sweden’s energy grid optimises efficiency.
In a mission statement, STEGRA announced:
“Being Europe’s first greenfield steel mill in 50 years, it will set a new benchmark for the industry. We will do things differently and produce green steel in a fully integrated production process, using end-to-end digitalisation, electricity from renewable sources, and green hydrogen. By replacing coal with green hydrogen and electrifying the steelmaking process, we will be able to cut CO2 emissions by up to 95% compared to traditional steelmaking. Moving forward, we will continue to reduce emissions even more – getting closer and closer to zero – year by year.”