Rosen Group: Hydrogen Competence for a Sustainable Future
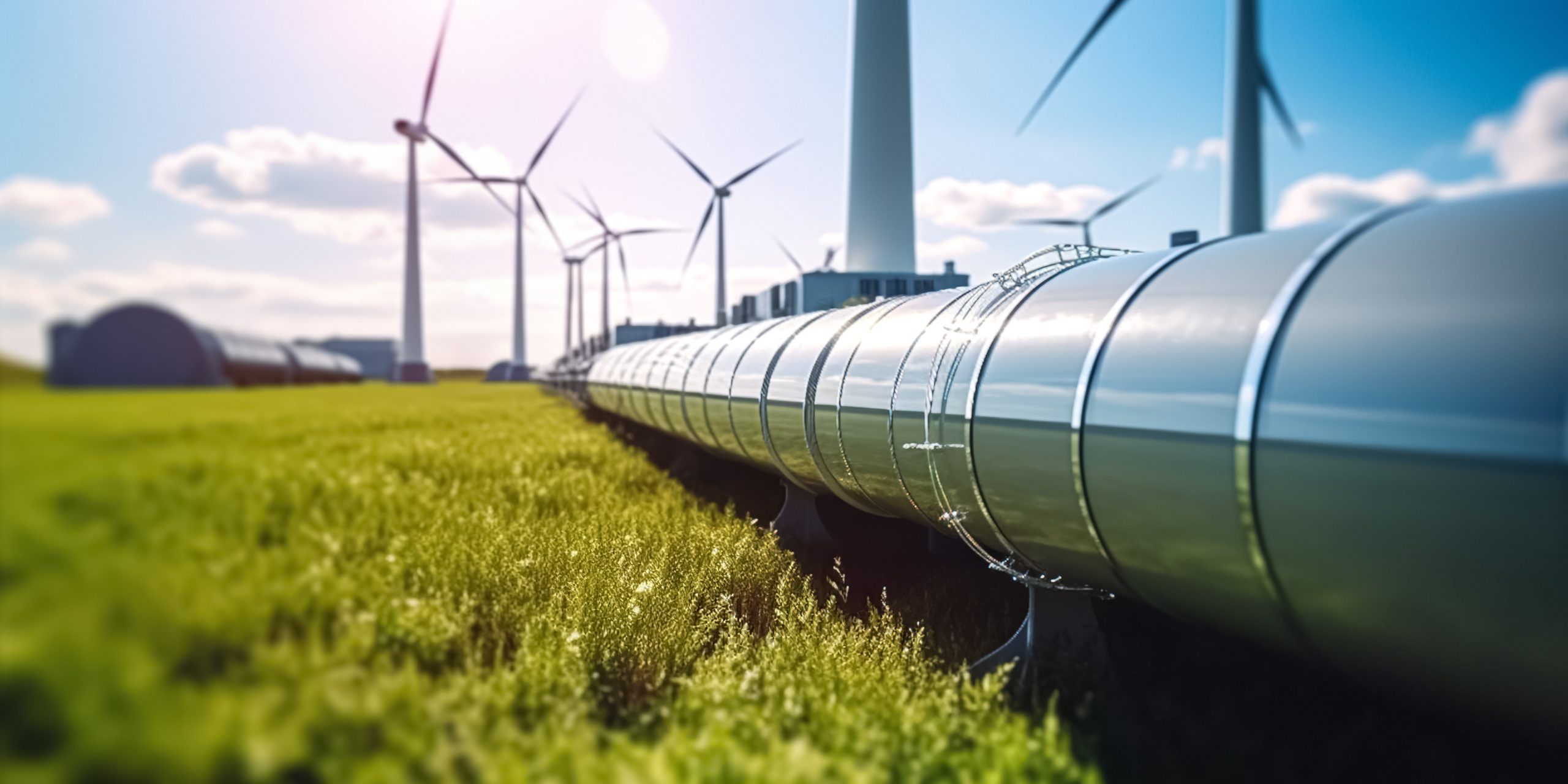
As the world moves towards a decarbonised future, global demand for energy continues to rise. Meeting the demand while simultaneously reducing overall emissions challenges the energy sector.
In this context, renewable hydrogen as a flexible energy carrier will be a key player in moving the industry forward. New and existing pipeline systems offer ideal conditions for storing, transporting and distribution increasing amounts of hydrogen.
Rosen Group supports pipeline operators in the process of converting their existing gas grids to hydrogen. This requires informed decisions for this mission.
Their many years of experience in all aspects of performance, safety, and security of pipelines ensure that they know what needs to be done for success in a hydrogen economy.
‘’Knowing the assets and their individual condition precisely is key to safely convert them. This is what we do all day in order to support operators in the best possible way.’’ – Neil Gallon, Principal Engineer, ROSEN Group
H2 competence: Data, experience and technology – all under one roof
Introducing hydrogen into an existing natural gas grid comes with some challenges. Whether completely converting an existing pipeline to hydrogen transportation or introducing a hydrogen blend, regulatory requirements dictate a series of preparatory actions.
Making this process digestible through our phased approach allows for a step-by-step guide, that, in the end, results in a hydrogen pipeline.
Pipelines transporting hydrogen are still pipelines, so all the threats operators face with natural gas lines are still relevant.
Therefore, pipeline operators will need to continue managing these threats. However, there are certain characteristics of H2 that may introduce new risks or increase the severity of existing threats due to the effect of hydrogen on the mechanical properties of steel.
In essence, hydrogen decreases ductility and fracture toughness and increases fatigue crack growth rates. This means that understanding existing cracks and the actual pipeline material properties in hydrogen becomes crucial for well-founded decision making.
Their dedicated phased approach has shown its value in numerous projects that were recently conducted. Each standardised step fills data gaps and ends with your go/no-go decision to allow for cost certainty while ensuring maximum safety for every conversion project.
Hydrogen materials testing
Hydrogen can have an adverse effect on the fracture and fatigue properties of steel. The magnitude of the effect can vary depending on steel grade and microstructure, concentration of H2, and other
factors. Therefore, integrity assessments need to be based on the material properties which Rosen Group investigates in their laboratory in Lingen, Germany, one of the world’s finest hydrogen laboratories.
Their executed projects show clearly: A data-based risk assessment enables customers to add another building block to their risk management in a hydrogen economy.
In-line inspection has been one of the most effective ways of gathering data points for the integrity management of pipelines. Their deep understanding of hydrogen allows for in-line inspections in hydrogen pipelines with any technology of their broad portfolio.
The latest sensor technologies detect hydrogen-related threats and defects to minimise potential risks. Every day they are trying to learn more about our most appropriate inspection solutions, either for new or converted hydrogen pipelines.
Byline: Petra Čotić